Cycle times in biomass feed hopper applications
Scope
Biomass energy systems require large equipment to reach economies of scale required to prove commercial viability as an alternative energy solution. The scale of the equipment is a considerable hurdle for the economic viability of commercial scale biomass energy from woody and non-food biomass feedstock. In order to reduce equipment size, cycle times must be shortened to allow for comparable throughput. Currently accepted norms require the use of large ball valves that are limited to 15 minute cycles. Shorter cycle times will increase wear beyond acceptable limits and risk premature valve failure. By decreasing the size of the valve, the equipment size can be reduced and the overall cost of the system may be reduced.
The Stargate-O-Port-Valve® is a full o-port design valve intended primarily in services where ball valves have poor reliability or other short comings. Cycle time limitations, whether it be reduction in wear to allow for a longer mean time between refurbishment matching an outage schedule or simply physical limitations of the valve
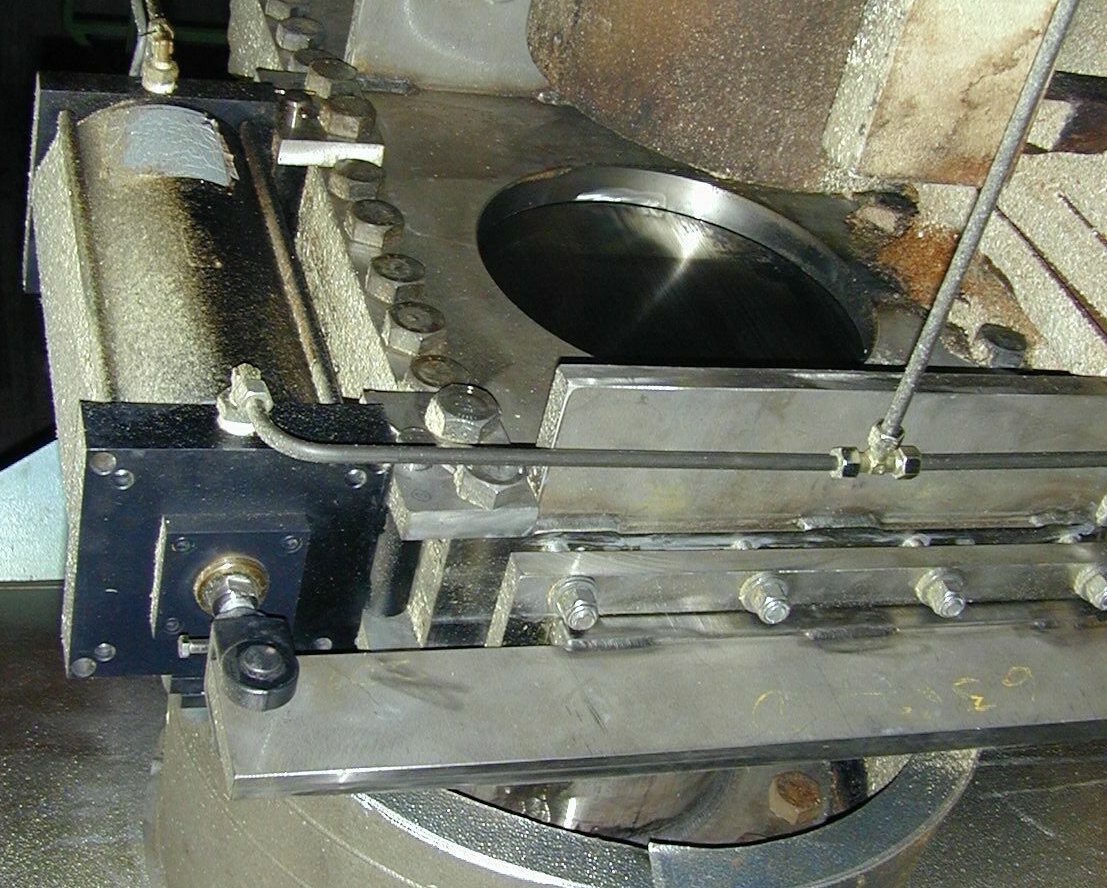
Considerations when establishing cycle time
- Feedstock characteristics
- Wear on seal components
- Required throughput for feed to downstream process
- Physical limitations of associated equipment (steam time, process reaction time, draining, vacuum, etc.)
Feedstock Characteristics: Feedstock varies from sawdust/fines, wheat straw, and bagasse, and mashed sugar beets. More dense materials will flow better and allow for shorter cycle times. Sawdust and fines allow for the shortest cycle times in this particular process. The longest cycle times are experienced with materials that do not flow well. Bagasse is the most difficult due to the stringy nature of the material. The material tends to jumble and will plug the hopper if fed too fast. As such, the cycle time is slowed.
Wear on seal components: Woody biomass is more abrasive than one would think. The wear on the seal components is exacerbated when the feedstock is not “clean”, i.e. higher sand/grit content. The more often the valve cycles, the more interaction there is between the selected feedstock and the seals of the valve. The limitation of ball valves is that the distance the ball travels over the seat is longer than that of the Stargate-O-Port-Valve®. The shortest distance between two points is a straight line with the valve seat in contact with the round surface of a ball, the wear, regardless of feedstock properties and conditions will be higher than that of a valve seat acting on a linear acting blade simply due to the distance traveled in contact with the mating surface.
Required throughput for feed to downstream process: An established volume of material is required to feed downstream equipment for process efficiency. In order to meet that volume, the hopper must be either very large or the hopper must cycle more frequently to supply the required feedstock volumes with a smaller hopper.
Physical limitations of associated process equipment: This component to the cycle time consideration is resolved relatively easily. Pressurization of the hopper, venting of the hopper following a feedstock injection, and material handling equipment’s ability to provide feed rates of the corresponding feedstock will be factors in the cycle time to be achieved. Also to be considered is the speed at which the valve can actuate from open to close and close to open.
Real world application
Process Overview: Hydrolysis process that requires an inlet lock hopper to feed material to the reactor without losing pressure in the reactor.
- The 12” 300# SG inlet valve opens to fill the hopper with process material.
- The 12” 300# SG inlet valve closes and the hopper is pressurized to reactor pressure.
- The 16” 300# SG outlet valve is opened to feed hopper content to the reactor.
- The 16” 300# SG outlet valve closes and a pressure relief, drain, or blow-off valve is opened to relieve hopper pressure.
- 12” 300# SG inlet valve is opened to re-start the hopper process.
Operating Conditions: The process operates at 225psig (397F) and reactor pressure must be maintained for process efficiency. The valves are operated under no pressure differential as is typical for lock hopper operations.
Cycle Times:
- Sawdust and fines: 3-5 minutes
- Wood chips: 4-6 minutes
- Sugar Beet: 3-5 minutes
- Wheat straw: 6 minutes
- Bagasse: 6 minutes
Valve performance:
The lock hopper valves were in continuous service for a period of 4 years. There were maintenance incidents that related to the valve:
- Solenoid valve failure. The solenoid valve was replaced and production continued.
- Snubbers on the outlet of the solenoids to control actuation speed. The snubbers would get gummed up due to the quality of the instrument air.
- Addition of packing on one valve. Nominal packing wear is to be expected particularly in higher cycle applications at elevated temperatures. Regular PMs were performed to adjust packing on the three valves. Depending on the accuracy of the PMs, i.e. not over tightening packing or leaving packing too loose, packing wear may be higher. One valve required addition of packing material which was done with the valve in line and the process offline, i.e. no system pressure.
The seal through the valve and from the valve body was maintained beyond the user expectation over the course of 4 years. The average cycle time was subjectively estimated at 3-6 minutes for 70% of the service life. 8-10 minute cycle times are subjectively estimated for the remaining 30% of the service life (slow feed rates of bagasse due to grinding process: material did not “flow”)
Recommendation for Cycle Times for the Stargate-O-Port-Valve® in biomass lock hopper applications
The limitation on the cycle time for the Stargate-O-Port-Valve® is the acceleration and deceleration of mass involved in the actuator piston and the blade of the valve and the pneumatic/hydraulic supply volume to the valve actuator(s) and the capacities of the automation equipment (solenoid/poppet valves, regulators, etc.).
There are Stargate-O-Port-Valves® in service that cycle every 13s. For biomass lock hopper applications, the cycle times vary by end user and feedstock. The shortest cycle times are 2-3 minutes and the longest cycle times are ~12 minutes under varying parameters of process conditions and feedstock materials. The valves cycling every 2-3 minutes have been in continuous service since April 2017. The valves from the real world example provided in this document cycle every 5-7 minutes for a majority of operation and have been in continuous service for 4 years.
For biomass lock hopper valves SVC recommends cycle times of 4-6 minutes to have a reasonable expectation for a mean time between refurbishment of at least one year. Longer mean time between refurbishment can be reasonably expected and will depend on the specific installation. This recommendation is not considering feed stock material flow characteristics and handling equipment capacities.
Please contact SVC with specific questions regarding cycle times for biomass lock hopper feed applications.