Antistik Valves
Anti-scale valve for sticky powders
Background
A customer contacted SVC about an application where the 4” 1500# segmented ball valves they were using at the time only lasted a maximum of 6 weeks. The valve had to be able to shut off against nitrogen gas at 750 psi and the highly scaling solid powder material.
The main reliability issue for the end user was the repeated damage to the highly polished ball and seat, leading to unacceptable leakage through the valves after less than 3000 cycles. The damage to the ball and seats stemmed from the powder material passing through the valve that firmly stuck/scaled to the valve components. At each actuation, further deposits of material lead to perpetual damage and premature wear to the valve seats and seals.
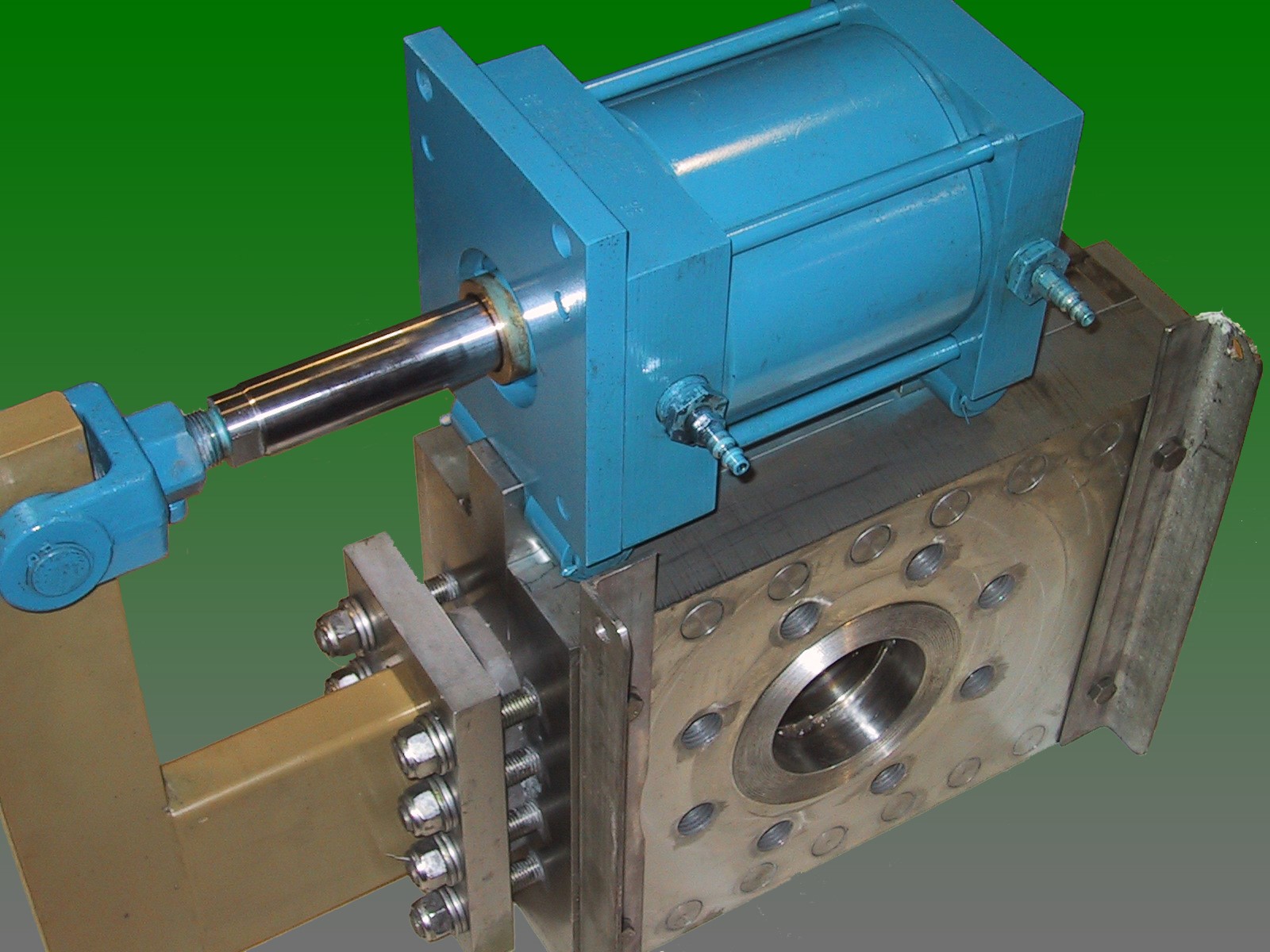
Stainless Valve Company Solution
Stainless Valve Company has developed custom specialty valves, based on the well-established Stargate-O-Port-Valve®, for applications in mining and pulp manufacturing, specifically for critical and demanding applications involving scale formation or sticky materials. Testing several combinations of seat materials and blade coatings in the lab at SVC, a combination was established that prevented the sticking/scaling of the powder to the valve blade and seats. Incidentally, the obvious answer was rejected as the material did scale up on PTFE. Preventing the accumulation of compacted powder layers on the blade and the seats gave proper sealing characteristics of the valve. The valve was run for 15000 cycles without showing any difference in performance and leak tightness. (Update August 2016: the valve has been in service for over 250k cycles with the only maintenance on the valve being the replacement of the actuator seal kit on two occasions.)
In 1996, because of an injury, one of our customers had contacted us to find out whether we have a solution for this problem. We devised the concept for the lime storage bin isolation valve. Since installation in 1997, the valve has been in continuous service and has made the operation of the lime storage bin more safe and reliable.
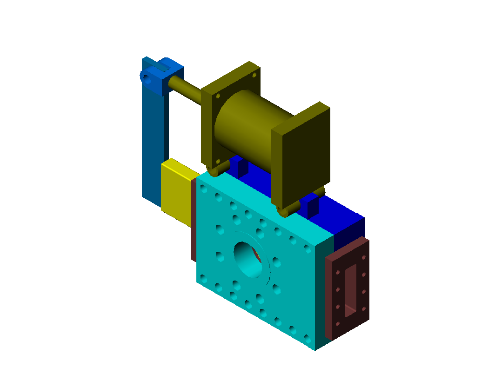
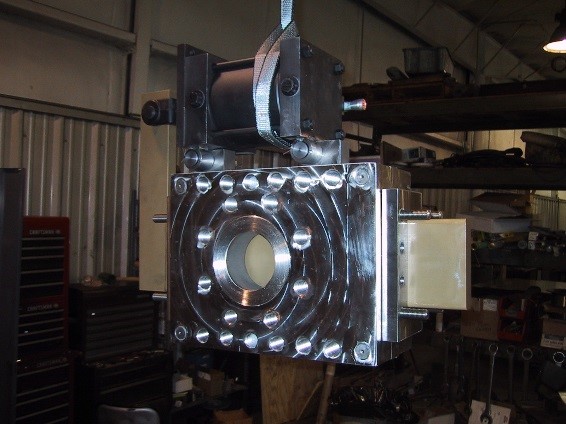
Partially assembled valve
Application Specific Challenges
The available space envelope for installation was tight and would not allow for the dimensions of the standard configuration of the Stargate-O-Port-Valve®.
Most engineers, at first glance, will state that the above design rendering is not possible. Most engineers will also state that a gate valve can never replace a ball valve in severe and critical service. This valve alone will prove both statements to be incorrect. Despite the optics of a large cantilever force or side load acting on the valve, the blade of the valve is so well guided between the blade guides in both ends of the valve body that this valve will actuate without difficulty or jamming due to cocking of the blade.
In 1996, because of an injury, one of our customers had contacted us to find out whether we have a solution for this problem. We devised the concept for the lime storage bin isolation valve. Since installation in 1997, the valve has been in continuous service and has made the operation of the lime storage bin more safe and reliable.